Технология обогащения железных руд
Сырьем для железорудных концентратов являются магнетитовые, гематитовые, гематитомагнетитовые и в меньшей мере бурожелезняковые и сидеритовые руды.
Качество концентратов для различных месторождений регламентируется соответствующими стандартами и техническими условиями.
Для месторождений КМА технические условия на магнетитовый концентрат предусматривают крупность 0,1-0 мм, влажность 10,5 %, содержание железа не менее 64 %. Для ряда концентратов регламентируется содержание вредных примесей: фосфора не более 0,08 %, серы не более 0,8 %.
Наиболее широко распространенную группу руд представляют магнетитовые кварциты. Основным рудным минералом в них является магнетит Fe3O4 и в незначительных содержаниях присутствуют гематит, мартит Fе2О3 и сидерит FeCO3. Пустая порода представлена кварцем SiO2.
Основным методом обогащения магнетитовых руд является магнитная сепарация, а в ряде переделов применяют промывку, отсадку и флотацию.
Технология обогащения магнетитовых кварцитов включает в себя, как правило, три-четыре стадии дробления до крупности 15-0 мм, три стадии измельчения до крупности 90 % класса -44 мкм, три стадии мокрой магнитной сепарации и три стадии обезвоживания концентратов.
Типовая технологическая схема обогатительной фабрики для переработки магнетитовых кварцитов представлена на рис. 13.2. Исходная руда из карьера крупностью - 1200 мм, содержащая порядка 30-35 % железа, поступает в конусную дробилку крупного дробления ККД-1500 на I стадию дробления до крупности -350 мм, а затем на II стадию дробления в конусную дробилку среднего дробления КСД-3000Т. Дробленый продукт второй стадии дробления крупностью -80 мм идет на грохочение по крупности 20 (15) мм. Надрешетный продукт крупнее 20 мм направляют на III стадию дробления в конусные дробилки мелкого дробления КМД-3000Т до крупности 20 (15) мм. Подрешетный продукт крупностью -15+0 мм объединяют с дробленым продуктом III стадии дробления и системой конвейеров транспортируют на склад усреднения и бункерования. После усреднения на складе дробленую руду посредством питателей и конвейеров направляют на сухое магнитное обогащение в барабанных сепараторах типа ПБС с получением отвальных хвостов и промпродукта для дальнейшего обогащения. Для более полного раскрытия рудного минерала промпродукт подвергают трехстадиальному измельчению. Первую стадию измельчения осуществляют в стержневой мельнице МСЦ3600x5500 до крупности -2 мм. Измельченный материал направляют на I стадию мокрого магнитного обогащения в барабанных магнитных сепараторах ПБМ-П-90/250. Хвосты выводят в отвал, а концентрат подвергают доизмельчению II стадии в шаровых мельницах МШЦ4500х6000 до крупности 65 % класса -44 мкм, классификации, и затем он поступает на II стадию мокрого магнитного обогащения. Хвосты направляют в отвал, а концентрат подвергают классификации, доизмельчению III стадии в шаровых мельницах МШЦ до крупности 90 % класса -44 мкм и направляют на III стадию магнитного обогащения. При необходимости вводят четвертую стадию магнитного обогащения. Хвосты третьей стадии обогащения идут в отвал. Кондиционный концентрат третьей стадии обогащения подвергают фильтрованию на дисковых вакуумфильтрах, после чего направляют на сушку в барабанные сушилки или на окомкование.
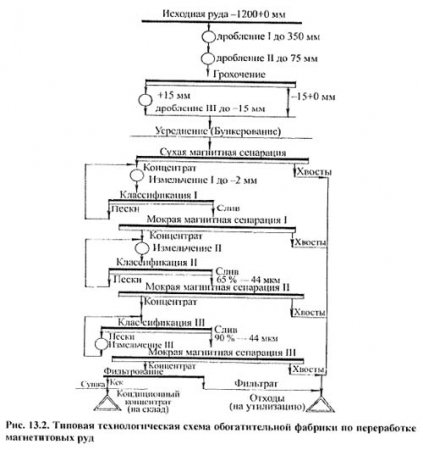
При содержании в исходной руде 34,9 % железа получают конечный концентрат с содержанием более 65 % и хвосты с содержанием менее 12 % железа. Извлечение железа в концентраты из руды составляет 81,0 %.
Обогащение гематитомагнетитовых, гематитовых, бурожелезняковых и сидеритовых руд осуществляют по комбинированным магнитно-гравитационным, магнитно-флотационным и гравитационным схемам.
Отходы обогащения могут быть использованы для получения щебня, песка, в ряде случаев для извлечения сопутствующих полезных компонентов, цветных и редких металлов.
- Технология обогащения руд цветных металлов (часть 3)
- Технология обогащения руд цветных металлов (часть 2)
- Технология обогащения руд цветных металлов (часть 1)
- Подготовка полезных ископаемых к переработке (часть 2)
- Подготовка полезных ископаемых к переработке (часть 1)
- Технология переработки и обогащения
- Окускование полезных ископаемых и продуктов обогащения (часть 3)
- Окускование полезных ископаемых и продуктов обогащения (часть 2)
- Окускование полезных ископаемых и продуктов обогащения (часть 1)
- Процессы обезвоживания (часть 2)
- Процессы обезвоживания (часть 1)
- Процессы радиометрического обогащения
- Процессы электрического обогащения (часть 1)
- Процессы электрического обогащения (часть 1)
- Магнитные сепараторы
- Процессы магнитного обогащения (часть 2)
- Процессы магнитного обогащения (часть 1)
- Флотационные машины
- Процессы флотационного обогащения (часть 2)
- Процессы флотационного обогащения (часть 1)
- Промывка
- Обогащение в потоке воды на наклонной плоскости (часть 2)
- Обогащение в потоке воды на наклонной плоскости (часть 1)
- Отсадка и отсадочные машины
- Обогащение в тяжелых суспензиях (часть 2)
- Обогащение в тяжелых суспензиях (часть 1)
- Машины и аппараты для классификации по крупности (часть 2)
- Машины и аппараты для классификации по крупности (часть 1)
- Классификация по крупности (часть 3)
- Классификация по крупности (часть 2)